スポーツまるごとHOWマッチBACK NUMBER
セルロイドは禁止…プラスチック製になった“卓球ボール”の厳格すぎるチェックが凄かった「打感を極限まで従来のセルボールに」
posted2022/07/17 06:00
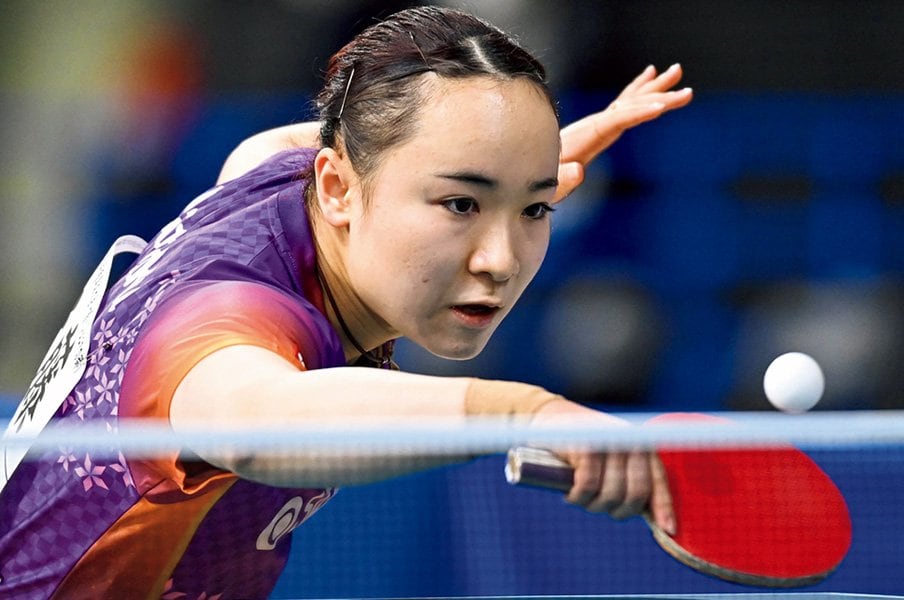
卓球のボール一個396円。ロンドン五輪以降、素材の変化に伴い、製造方法も大きく変わった
text by

熊崎敬Takashi Kumazaki
photograph by
KYODO
カラーボールの登場を除けば、まったく変化がないように見えるピンポン球。2012年ロンドン五輪後、素材がセルロイドからプラスチックに変わったことは、あまり知られていない。発火性が高いセルは危険物扱いのため、飛行機への持ち込みが禁止。プラになれば、機内持ち込みが可能になる。
ITTF(国際卓球連盟)の“セル禁止令”により、各国のメーカーは素材の見直しを迫られることになった。このとき最大手のニッタクに白羽の矢を立てられたのが、前職で化粧品容器を手がけ、プラ成形を熟知する高田道明さん(現・古河工場長)だ。
「卓球ボールには厳格な規格があり、すべてをクリアしないと国際公認球の証であるスリースターはもらえません。しかし重さや硬さ、バウンドなど、こっちを満たすとあっちが欠けるというイタチごっこのような状態が続きました。規格を満たすだけでなく、打感を極限まで従来のセルボールに近づけないといけない。結局ABSという樹脂に落ち着きましたが、完成まで2年近く試行錯誤しました」
セルボール時代は職人の感覚頼みだった
新素材の選定に加え、高田さんは会社から求められた製造工程の簡略化も実現する。
実際に工場で見せてもらった製造工程は、(1)ABS射出、(2)成形、(3)研磨、(4)乾燥、(5)重量検査、(6)抗ウイルス・抗菌コーティング、(7)外観チェック、(8)印刷、(9)箱詰めと9段階に分かれるが、ひとの手によるのは最後の箱詰めだけ。残りはすべて機械で行なわれる。
中でも特筆に値するのが(7)外観チェック。
「ここでは画像検査機という機械で1球につき64回シャッターを切り、異物や傷の有無、寸法や真球度を厳格にチェックし、良品、不良品、再検査の3つに分けていきます。不良品は練習ボールとして使用されます」
ちなみにセルボール時代、外観チェックは研ぎ澄まされた感覚を持つ職人の透視検査という形で行なわれていた。
「入社したばかりのころ、ボールを凝視する職人さんたちを見て、こんなアナログな世界がまだあるんだと驚いたものです」
素材が変わり、機械化が進んだ製造プロセス。これによって2カ月かかっていた製造日数は、1週間前後と大幅に短縮され、同時に良品率も約8割に向上した。3個セットで税込み1188円、1球あたり396円の「3スタープレミアム クリーン」は、こうして今日もひとけのほとんどない工場で1日に約5000ダース生まれるのである。
